Subchapter 3.8
Safe enabling functions
In cases where guards hinder operation or monitoring is impractical, providing operators with push-buttons, foot switches, or two-hand controls ensures safe starting and stopping of hazardous situations. With the following information we will explain and discuss the different options and their advantages.
Alternative 1
Two-hand control
Two-hand control is sometimes referred to as “two-hand start,” meaning that two buttons must be pressed simultaneously or within a short time span (0.5 seconds) to initiate the movement of a hazardous machine part.
The term "two-hand start" may cause designers to overlook a crucial requirement: the operator must continue pressing the buttons until the hazard is eliminated. If the operator releases one or both buttons prematurely, the operator could potentially reach the hazard zone and be injured.
To prevent this, the two-hand control buttons must be positioned at a calculated safety distance. This ensures that it is impossible to reach the hazard zone before the moving parts have completely stopped. The correct standard for these calculations is (EN) ISO 13855.
Consider the following additional factors when designing two-hand control:
- Be aware that two-hand control can only “protect” one person (or one person per panel), so if two people are working together, they could still be at risk of injury.
- Since only one person is protected, access to the hazard zone must be restricted as much as possible (e.g. through guards).
- The operator starts a dangerous movement that might present a hazard to others. So he needs full view of the hazard zone.
The international standard for two-hand control systems is (EN) ISO 13851. This standard is also referenced in ANSI B11.19 for the USA and CSA Z432 for Canada.
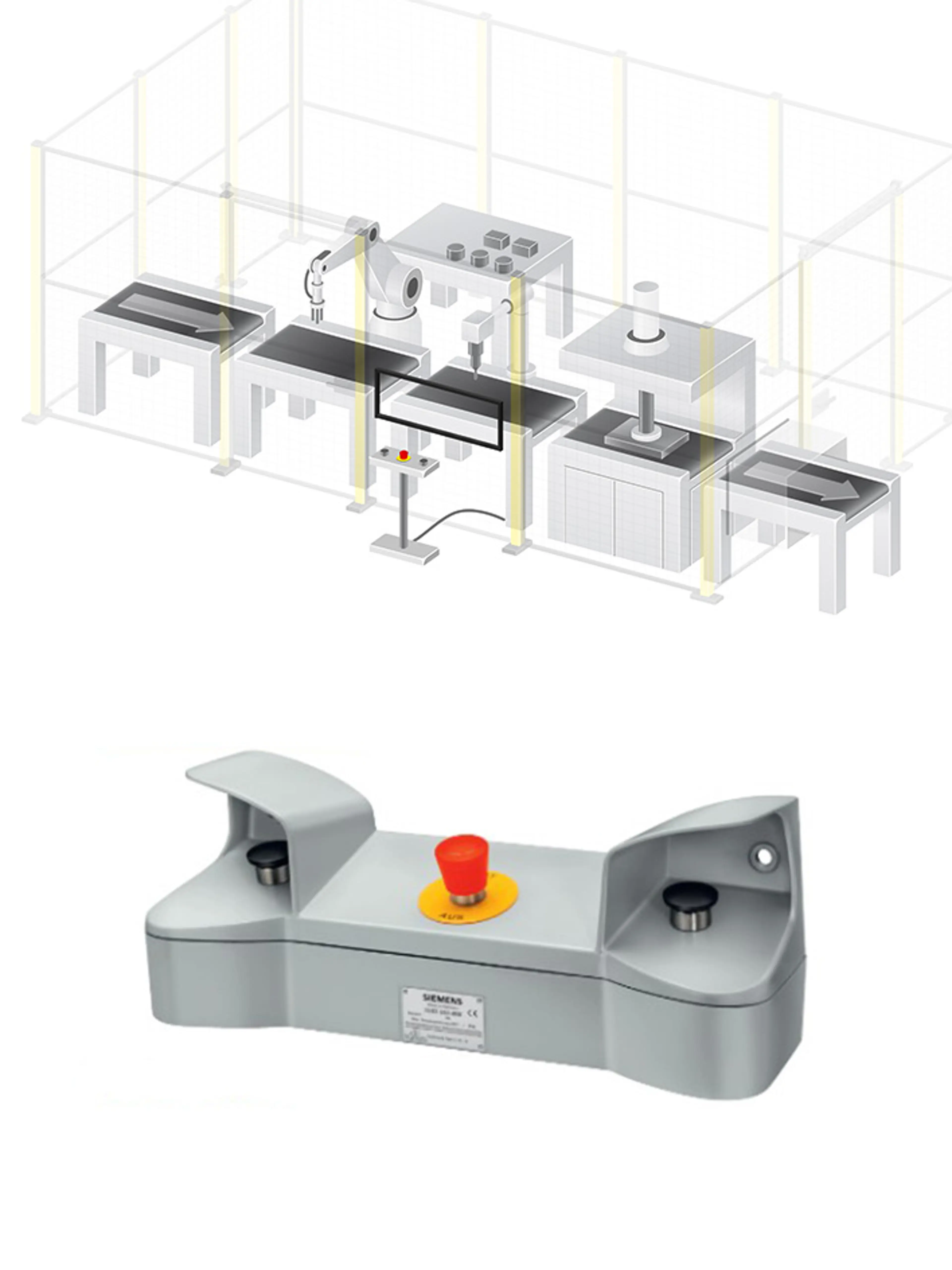
Alternative 2
Hold-to-run, enabling, and manual control
Another frequently used way of giving people control of the hazard is the so called “hold-to-run” device.
This typically involves a button (hardware or on-screen) that triggers a movement or function as long as it is pressed or touched. This way, the operator can determine when the hazard occurs and when it is to stop.
The same principle applies to manual control. However, it is not usually considered a safety function. For instance, a hand drill features manual control, but one would hardly consider the possibility to let go of its trigger as a safety function.
Hold-to-run safety functions can come in two different forms:
- Direct Control: Using only a single push-button.
- Indirect control: Involving an on-screen button and an "enabling" button. The on-screen button is active only when the enabling button is also pressed. This differs from two-hand control, where simultaneous pressing is monitored. Here, the two buttons only need to be pressed in sequence. Releasing the enabling button stops the hazardous movement.
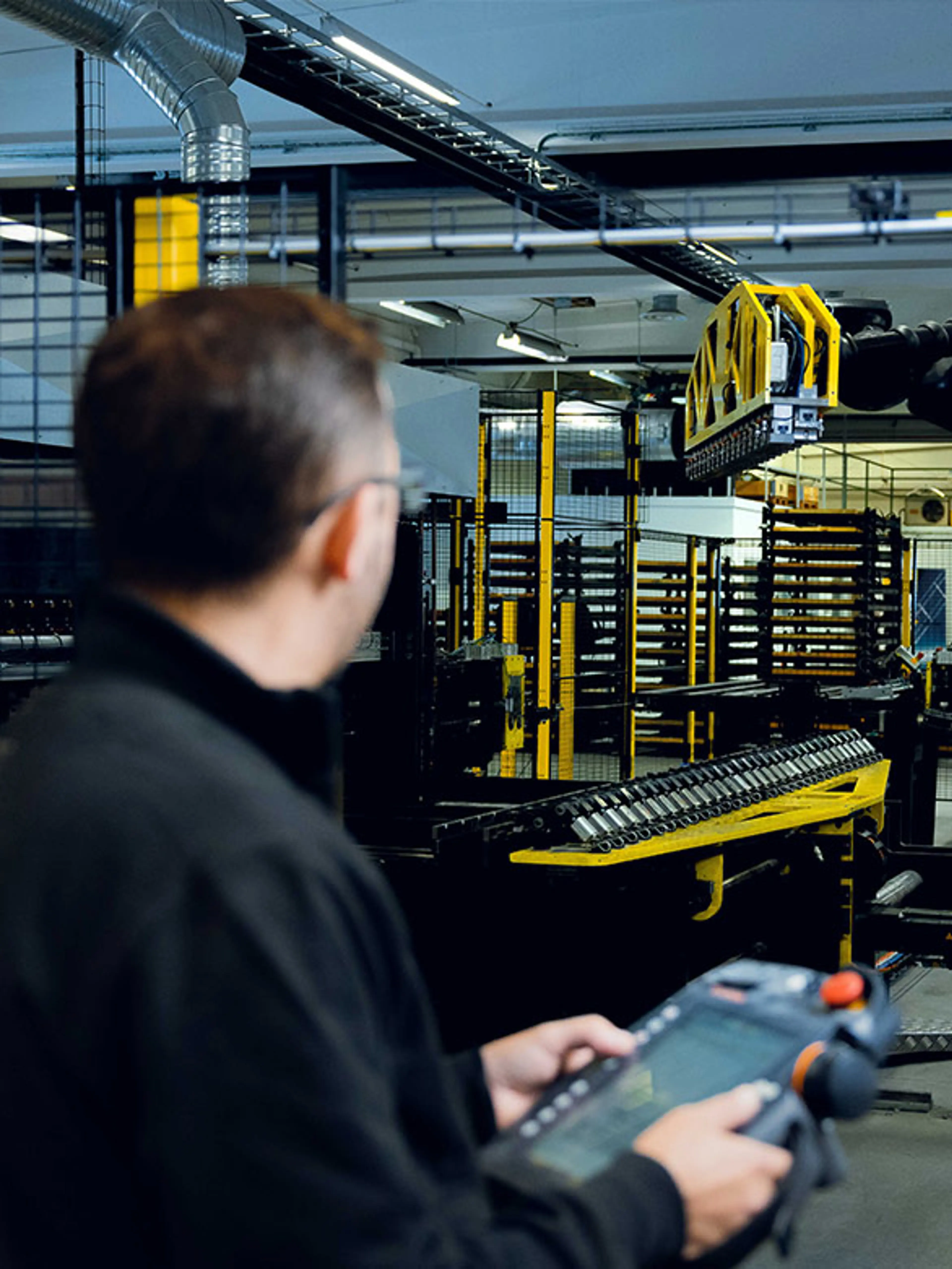
Requirements for correct design of hold-to-run functions
Four major requirements for a hold-to-run function are sometimes overlooked:
- Control Mode: Hold-to-run can only be used in a separate, selectable control mode. It must not be part of an automatic operating cycle.
- Immediate Stop: Releasing the hold-to-run or enabling button must stop the hazardous movement as quickly as possible.
- Motion Control: The motion speed, force, or stroke must be limited so the operator can realistically release the button in time to remain safe. This is often not the case with manual control, making handheld machinery like drills and chainsaws particularly hazardous.
- Escape Provisions: There must be a means of escaping the hazardous situation, such as a mobile panel, limited access (keeping the operator away from the actual hazard source), or, in most cases, an emergency stop button nearby. Most enabling switches have a built-in emergency stop button.
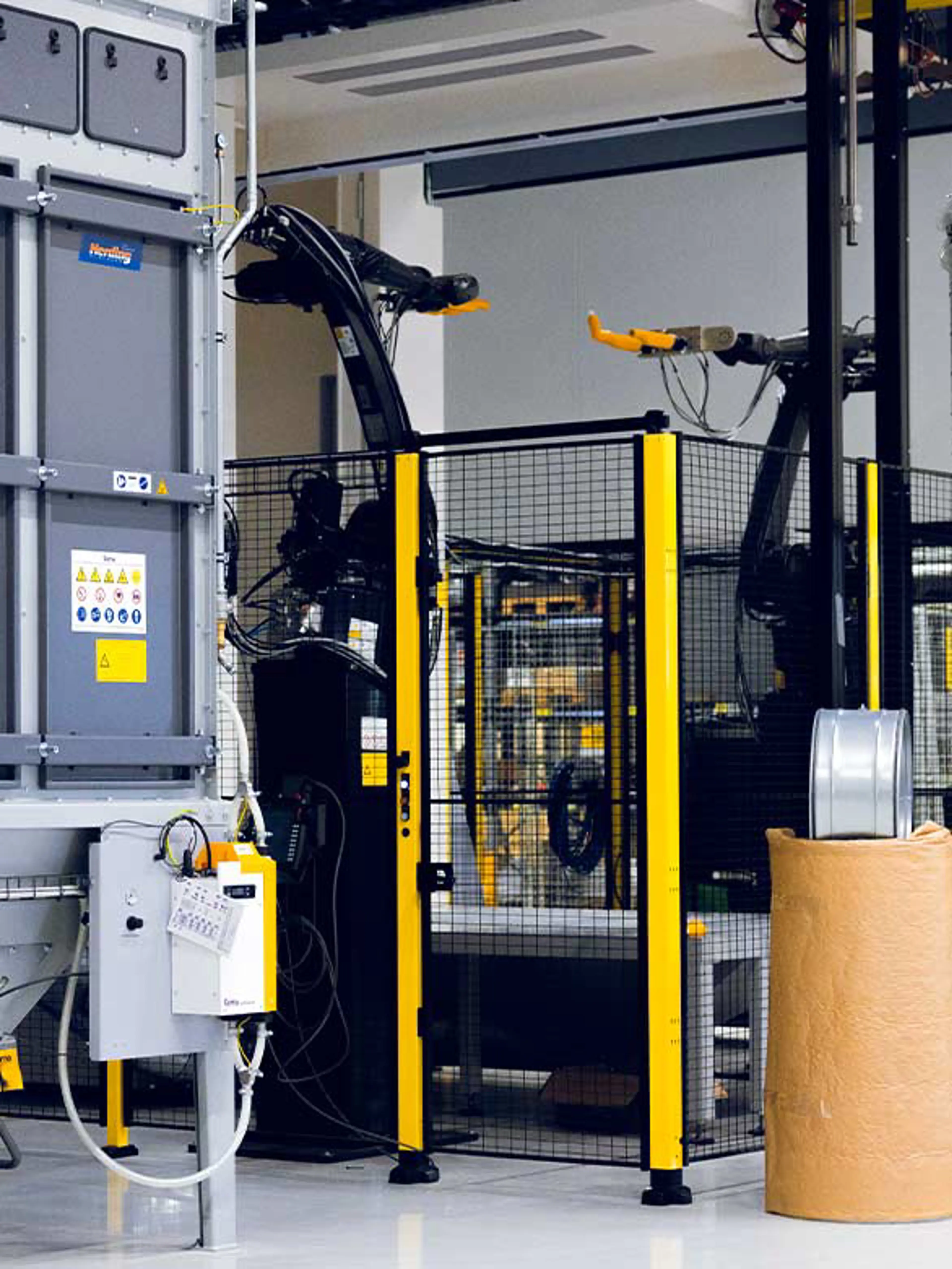